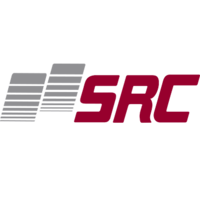
Description
Monday-Friday 8:00am-4:30pm
POSITION SUMMARY:
Reporting to the Program Director, this position will serve as the central control for all environmental, health and safety issues for Genie Reconditioning, LLC.
ESSENTIAL JOB FUNCTIONS:
- Provide OSHA compliance guidance on processes, equipment, supplies, and environmental matters
- Recommend measures to protect workers from potentially hazardous work methods, processes, or equipment
- Develop safety programs and objectives, as well as coordinate/conduct training programs
- Prepare, review, and update environmental investigations and recommendation reports
- Provide technical-level support for environmental remediation projects, including remediation system design and determination of regulatory applicability
- Monitor progress of environmental improvement programs
- Identify hazardous materials that need to be removed, using monitoring devices
- Provide accurate record-keeping activities for Occupational and Environmental reporting
- Lead Safety Committees to make positive changes in the organization
- Identify and select proper Personal Protective Equipment for machines, processes, and environment
- Ensure Hazardous Communication is both established and effective
- Understand and administer Worker's Compensation and the processes involved including reviewing physicians' reports, therapies, final ratings, etc.
- Ensure that all regulatory notices are communicated and followed
- Track lost-time injuries, days restricted duty, and incident frequency and severity
- Investigate all injury/illness and non-injury incidents to determine root-causes and follow-up as necessary
- Compile, analyze, and interpret statistical data related to occupational illnesses and accidents
- Coordinate environmental testing such as air sampling, noise pollution, lighting, hazardous waste, etc. when necessary
- Examine contractor credentials, licenses, or permits to ensure compliance and liability
- Coordinate periodic facility audits
- Function as emergency coordinator and create emergency response plans and business continuity initiatives
MINIMUM QUALIFICATIONS PREFERRED:
- BS/BA in Safety or related discipline required
- Three (3) years or more of previous Safety experience
- Three (3) years or more safety experience in a manufacturing setting is preferred
- Excellent verbal and written communication and presentation skills. The ability to listen to and understand information and ideas presented through spoken words and sentences. The ability to read and understand information and ideas presented in writing
- Must have the ability to multi-task by managing multiple projects at any given time
- Requires effective relationship management skills with co-workers in a team environment
- Ability to resolve conflicts including — Handling complaints, settling disputes, and resolving grievances and conflicts, or otherwise negotiating with others
- Encouraging and building mutual trust, respect, and cooperation among team members and associates
- Requires effective time management skills, personal conduct, and change management abilities
- Expanding personal competencies and capabilities through training and education is expected. Keeping up-to-date technically and applying new knowledge to your job
- Working knowledge of Word, PowerPoint, Excel, e-mail, and Web-enabled applications
- OSHA 501 Trainer
- First Aid and SPR Certified
- Hazardous Waste Management Certificate
- Heavy Machining and Fabrication Experience
- Ability to travel with occasional overnight stays
GENERAL RESPONSIBILITIES:
- Ensure all QMS (Quality Management System) guidelines and regulations are followed
- All employees are required to follow and promote all company and regulatory safety and environmental standards and exhibit safe work practices at all times
- Use of PPE (Personal Protective Equipment): Safety Toe Shoes, Safety Glasses, etc. required at all times in warehouse environment
- Follow established departmental policies, procedures, objectives, and continuous quality improvement objectives
- Actively participate in and support the principles of Open-Book Management
- Possess a positive attitude and promote a positive work environment
WORK ENVIRONMENT:
Work is performed in a manufacturing setting. The performance of this position may occasionally require some exposure to atmospheric conditions such as dust, fumes, noise, and varying temperatures for short periods.
PHYSICAL DEMANDS:
Limited physical effort with lengthy work cycles: Standing/Walking 40%, Sitting 60%. Ability to lift and carry up to 50 pounds is required.
Apply on company website