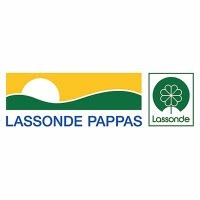
Description
SIGN-ON BONUS!
This position is eligible for a $1,000 sign-on bonus.
Want to learn how to make juice? Lassonde Pappas & Co. is a US Leader in beverage manufacturing dedicated to our team members, customers and consumers satisfaction. We remain committed to our small-town roots and rural values. Hardworking and caring are qualities that make our teams special. Since 1942, we've been producing delicious products for our customers across the country!
To provide the best for our customers, we focus on building the best team by creating and advancing an inclusive environment amongst our diverse workforce. If you're passionate about customer satisfaction, reliable, and committed to being and doing better, join us!
We value each of our employee's total wellbeing. To support employees in all stages of their wellness journey, we have a robust benefits program including: medical, dental, and vision coverage options, growth and development potential, along with 401-K, Life & Disability Insurance, PTO, Tuition Reimbursement, Health Fairs, Gym Membership Discounts, and so much more!
POSITION SUMMARY
The Lead Refrigeration Mechanic / PSM Coordinator reports to the Plant Manager and is based out of our Hendersonville, North Carolina location. This individual will be responsible for maintaining, servicing, and repairing Refrigeration equipment including completing PMs and work orders. This role is responsible for maintaining a compliant PSM and RMP program at the facility.
The Lead Refrigeration Mechanic / PSM Coordinator will develop, or assist in developing, organizing, scheduling, and conducting training programs for the refrigeration system, and hazardous materials team. Develop and review the SOPs for the refrigeration system, and ensure that all P&IDs are up to date. Review all PMs for mechanical Integrity compliance, and ensure that all piping is labeled and valve numbers are in place and accurate.
This role is responsible for maintaining all PSM documentation and training records that pertain to the PSM & RMP program, organizing, scheduling, and conducting PSM meetings, compiling and maintaining PSM action item logs, and assisting in completing items on the action item log.
PRIMARY RESPONSIBILITIES (essential functions of the job)
Reasonable accommodations may be made to enable individuals with disabilities to perform essential functions.
Responsibilities include:
- Maintains and services mechanical equipment, machinery, and components
- Uses Lathe, Milling Machine, Tig / Mig / Arc welders, CNC, and power tools as required
- Perform repairs and scheduled maintenance to mechanical, pneumatic, hydro, and electrical equipment. This includes facility and wastewater systems
- Proficient in electrical. 120/230vac single phase, 480vac three-phase, and AC/DC control voltages. Wiring diagrams, troubleshooting, and installation.
- Identifies and orders parts needed for replacement, creates work order, and performs repairs as necessary
- Performs the installation, maintenance, testing, troubleshooting, and repair of equipment to ensure optimum usage and quality
- Ensure compliance with company and regulatory requirements
- Schedules and coordinates contractor's installation support and service operations as needed
- Completes all work in accordance with established safety procedures
- Uses and maintains equipment manuals, completes work orders and inspection reports, documents work hours and other administrative tasks as required in CMMS
- Performs other related duties as required and on call during off shifts as needed
- Hazwoper Team Member after 24hr Hazwoper Training completed
- PSM Coordinator
- Ensures compliance with PSM and Risk Management Plan (RMP) and all local, state, and federal regulations.
- Review system-altering processes prior to implementation.
- Organizes and provides PSM-mandated training to all applicable associates and contractors.
- Reviews and assists with Management of Change (MOC), Pre-Startup Safety Reviews (PSSRs), and Process Hazards Analysis (PHA)
- Review all refrigeration action plans for ammonia-related projects to ensure compliance and viability with the PSM program
- Organizes and provides leadership concerning all 14 elements of PSM by reading and reviewing mechanical and electrical drawings, procedures, and ammonia-related programs and policies.
- Serves as a primary respondent in the event of any PSM audit activity.
- Actively participates in refrigeration team activities and programs, and works to improve skills by staying abreast of current technologies.
- Schedules refrigeration associates for PSM training and Confined Space, HAZMAT, and Hot Work training programs.
- Fit Test Administrator
- Fit Test and certify respirator users
- Provide feedback to managers on individual and team performance
- Accountable for food safety, food quality, and regulatory requirements for their position
- Encouraged to notify management about actual or potential food safety issues
- Adopt and maintain all SQF requirements for their position
- Empowerment to work with supervision to resolve food safety and food quality issues within their scope of work
- Train new employees that are hired in the work area assigned
- Advanced knowledge of the field
- Lead by example and assist others who may need guidance
- Be accessible for employees to ask questions regarding areas of expertise
- Provide positive recognition to employees who exhibit good behavior in their work area
- Provide feedback to managers on individual and team performance
- Perform other related duties as required and assigned
EDUCATION AND EXPERIENCE
Minimum Required Qualifications
- High School Diploma, or equivalent
- Three years of mechanic experience
- Three years of experience in Welding/Fabrication/Machining
- Excellent verbal and written communication skills
- Detail-oriented, can multi-task and manage projects
- RETA Certification Level 2 minimum
- Excellent time management skills
- PSM/RMP Training
- Must have excellent verbal and written communication skills
- Must be detailed oriented and have the ability to multi-task
- Proven organizational skills
Additional Preferred Qualifications
- Experience in the food/beverage industry
- Previous experience in Manufacturing or production environment, a plus
- Ability to direct, coach and train others
- Project management with contractors as needed and problem-solving skills
- Refrigeration Technician Training , Operator I,II
- Respirator Fit Test Training
PHYSICAL REQUIREMENTS & WORKING CONDITIONS
This position requires sufficient physical ability to work in a typical manufacturing setting.
FREQUENT: Ability to talk and hear; ability to stand, walk, climb stairs, stoop, bend and/or crouch; push/pull; lift up to 50 pounds; use of hands and fingers to operate machinery/equipment and all manual and electronic equipment in area of responsibility. Exposure to wet and humid conditions and fluctuations in ambient temperature (seasonal).
OCCASIONAL: Squatting, kneeling, ability to reach above and at shoulder height. Ability to wear a dust mask, and perform Confined Entry using LOTO program. Exposure to toxic and corrosive chemicals.
VISION: Ability to use close and distance vision, as well as color and peripheral vision with or without correction. Must be able to visually detect obstacles and potential dangers in a fast-paced production environment involving high speed equipment and powered industrial lift equipment.
HEARING: Ability to hear in the normal audio range with or without correction. Exposure to noise levels from pumps, machinery, forklift traffic, bottle lines and exhaust fans.
This job description is not intended to contain a comprehensive list of the responsibilities that are required to successfully perform in this position. Other duties as assigned are part of every job description. The conditions herein are representative of those that must be met by an employee to successfully perform the essential functions of this job. Reasonable accommodations may be made to enable individuals to perform the essential job functions.
Lassonde Pappas & Co., Inc provides equal employment opportunities to all employees and applicants for employment and prohibits discrimination and harassment of any type without regard to race, color, religion, age, sex, national origin, disability status, genetics, protected veteran status, sexual orientation, gender identity or expression, or any other characteristic protected by federal, state or local laws.
This policy applies to all terms and conditions of employment, including recruiting, hiring, placement, promotion, termination, layoff, recall, transfer, leaves of absence, compensation and training.
Apply on company website